- Sheets should ideally be stored in controlled of humidity at RH 45-55% and temperatures at 20-25o C
- Sheets should be stored in a clean environment which is free from any industrial and chemical pollution which can chemically effect the sheet
- Sheet should be stored horizontally on a firm base to prevent warpage
- Sheets which are to be processed should be kept under above controlled conditions for 48 hours before processing
SPECTACLE FRAMES
RECOMMENDATION FOR PROCESSING CELLULOSE ACETATE SHEET FOR SPECTACLE FRAMES
Storage of Sheets
Effect of moisture on the physical and mechanical properties of the sheet
- High water content makes the material supple, increases the impact resistance but decreases thermal resistance
- Sudden heating of the material can cause formation of bubbles in the sheet from the moisture in the material
- Excessive drying or dessication can make the material fragile and prone to fracture
- Dimensional characteristics of the sheet can change with the change in the relative humidity
- Dessication can reduce the weight of the sheet, which will increase with rehydration
Milling of spectacle front
- Sheet slab should be properly clamped during milling process as vibrations can fracture slab
- Cutting angle of milling tool should be optimized. If angle is too steep, it can fracture material or cause irregularity of the milled surface. If angle too shallow it can cause overheating of material or strong vibrations during milling
- RPM and linear milling speed should be optimized (see table of relationship between linear speed versus RPM)
- If speed too high, it can chip or break the material
- If repetitive breaking occurs at same point this is caused by way of cutting. In this case change cutting RPM and speed
- I chipping occurs in certain operation, reduce the linear speed, don’t use new or recently sharpened tools, or hydrate the material in water for 12 hrs (adjust for final measurement as the material would have expanded
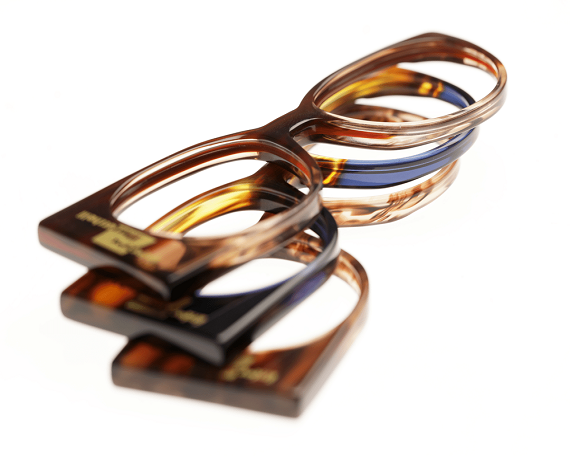
Results of milling tests on slab at different tool RPM and linear tool speed.
Rotation of tool RPM | Linear Speed Mtr/ min | Result |
---|---|---|
18000 | 3.5 -5.0 | No defect |
24000 | 4 | No defect except after extensive usage of tool |
16000 | 8 | Chipping at particular point |
16000 | 10 | Chipping at particular point |
12000 | 8 | Breaking or trimming |
Bonding of nosepad
- Bonding is generally done with acetone solvent, methyl acetate or a mixture of both. 5% Cellulose Acetate is added to the mixture which is left for 24 hrs to dissolve completely.
- Mixtures of solvents containing low concentration of ethyl acetate, methyl acetate (10-20%) or water (5-10%) gives better results than pure acetone (100%)
- Surface to be bonded should be cleaned and smooth
- To obtain perfect sticking without bubbles, put pressure for 5-10 secs and let material dry for 24 hrs
- Solvent bonding is being replaced with high frequency welding or friction welding techniques, which are quicker and give better finish, but are more expensive
Bending of nose bridge / toric curve
Most frequently used heating systems for bending nose bridge and toric curve area are :
- Temperature controlled infrared rays
- Liquid bath of DM water (50%) and glycerin (50%)
- Localised high frequency system
To get a stable bend the material should be heated to a temperature where the built in stress memory in the material is released and removed. The approximate temperature of heating is 110 C. Below this temperature, the bend will not be stable. All the above methods will give good results if the part is heated uniformally and for a sufficient period of time for the core of the part to get heated.
Barrel polishing of frame
A four stage process is recommended as follows :
- Rough Polishing – 12 hrs with Birch wood chips, pumice powder and oil
- Polishing – 12 hrs with birch wood chips, pumice powder and oil
- Polishing – 18 hrs with diamond / cube / pointed shape chips and polishing past
- Shinning – 18 hrs with diamond / cube / pointed shape chips and polishing past
Barrel construction
Barrels should be properly vented. If venting is not adequate, there could be a temperature buildup which can cause breakage or deformation of the part Barelling should ideally be done at 18-20o C
Degreasing
After each polishing stage, parts should be washed with neutral detergent solution with ultrasound to remove residue from the previous stage.
Polishing and finishing of frame
The frame can be polished by surface treatment with acetone vapour.
- The frame should be suspended in acetone vapour for less than 1 second.
- If it is exposed for very long, the material will expand and crack.
- The operating should be carried out in non humid conditions
- under no circumstances should the frame be directly dipped in the acetone liquid.